
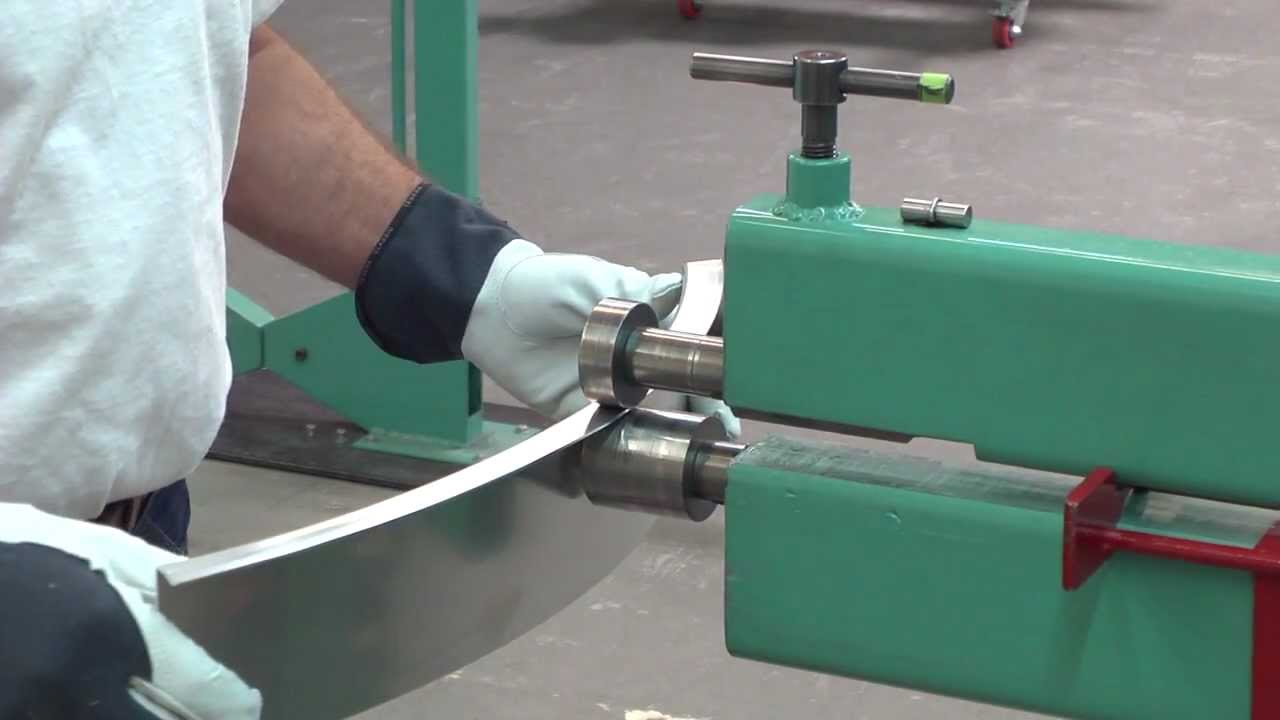
The acid blocks the negative charges in the polyacrylate gel so that they no longer repel each other, causing the gel to contract.

Once the desired molecules are attached in the right locations, the researchers shrink the entire structure by adding an acid. In this way implosion fabrication can create all sorts of structures, including gradients, unconnected structures, and multimaterial patterns,” Oran says. Then, you can develop that latent image into a real image by attaching another material, silver, afterwards. “It’s a bit like film photography - a latent image is formed by exposing a sensitive material in a gel to light. “It could be a quantum dot, it could be a piece of DNA, it could be a gold nanoparticle.”
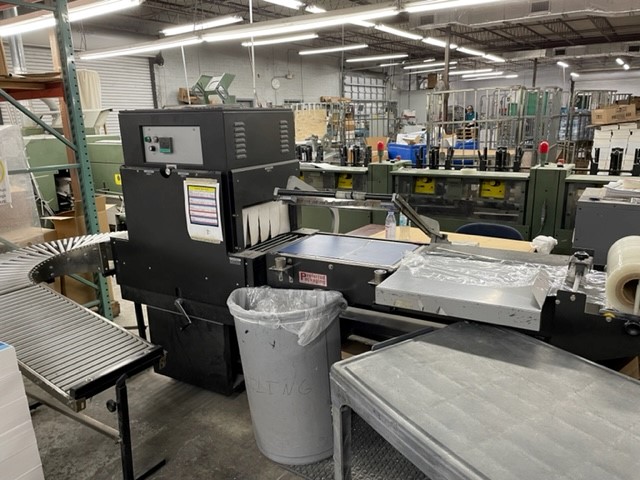
“You attach the anchors where you want with light, and later you can attach whatever you want to the anchors,” Boyden says.
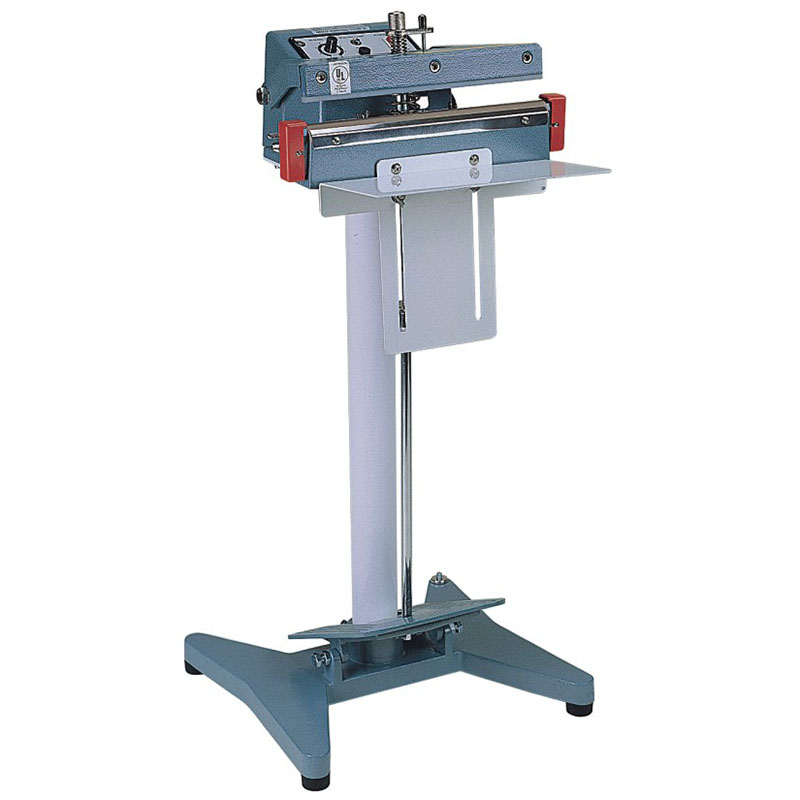
The fluorescein molecules act as anchors that can bind to other types of molecules that the researchers add. Using two-photon microscopy, which allows for precise targeting of points deep within a structure, the researchers attach fluorescein molecules to specific locations within the gel. The scaffold is bathed in a solution that contains molecules of fluorescein, which attach to the scaffold when they are activated by laser light. Hundreds of research groups in biology and medicine are now using expansion microscopy, since it enables 3-D visualization of cells and tissues with ordinary hardware.īy reversing this process, the researchers found that they could create large-scale objects embedded in expanded hydrogels and then shrink them to the nanoscale, an approach that they call “implosion fabrication.”Īs they did for expansion microscopy, the researchers used a very absorbent material made of polyacrylate, commonly found in diapers, as the scaffold for their nanofabrication process. This technique, known as expansion microscopy, involves embedding tissue into a hydrogel and then expanding it, allowing for high resolution imaging with a regular microscope. To overcome these limitations, Boyden and his students decided to adapt a technique that his lab developed a few years ago for high-resolution imaging of brain tissue. (The technique can yield a solid pyramid, for example, but not a linked chain or a hollow sphere.) Furthermore, they can only generate self-supporting structures. And, while methods exist that can directly 3-D print nanoscale objects, they are restricted to specialized materials like polymers and plastics, which lack the functional properties necessary for many applications. It is possible to make 3-D nanostructures by gradually adding layers on top of each other, but this process is slow and challenging. Etching patterns onto a surface with light can produce 2-D nanostructures but doesn’t work for 3-D structures. The other senior author is Adam Marblestone, a Media Lab research affiliate, and the paper’s lead authors are graduate students Daniel Oran and Samuel Rodriques.Įxisting techniques for creating nanostructures are limited in what they can accomplish. The technique uses equipment that many biology and materials science labs already have, making it widely accessible for researchers who want to try it.īoyden, who is also a member of MIT’s Media Lab, McGovern Institute for Brain Research, and Koch Institute for Integrative Cancer Research, is one of the senior authors of the paper, which appears in the Dec. These tiny structures could have applications in many fields, from optics to medicine to robotics, the researchers say. After attaching other useful materials to the scaffold, they shrink it, generating structures one thousandth the volume of the original. Using the new technique, the researchers can create any shape and structure they want by patterning a polymer scaffold with a laser. Eva Tan Professor in Neurotechnology and an associate professor of biological engineering and of brain and cognitive sciences at MIT. “It’s a way of putting nearly any kind of material into a 3-D pattern with nanoscale precision,” says Edward Boyden, the Y. They can also pattern the objects with a variety of useful materials, including metals, quantum dots, and DNA. MIT researchers have invented a way to fabricate nanoscale 3-D objects of nearly any shape.
